Masterbatch
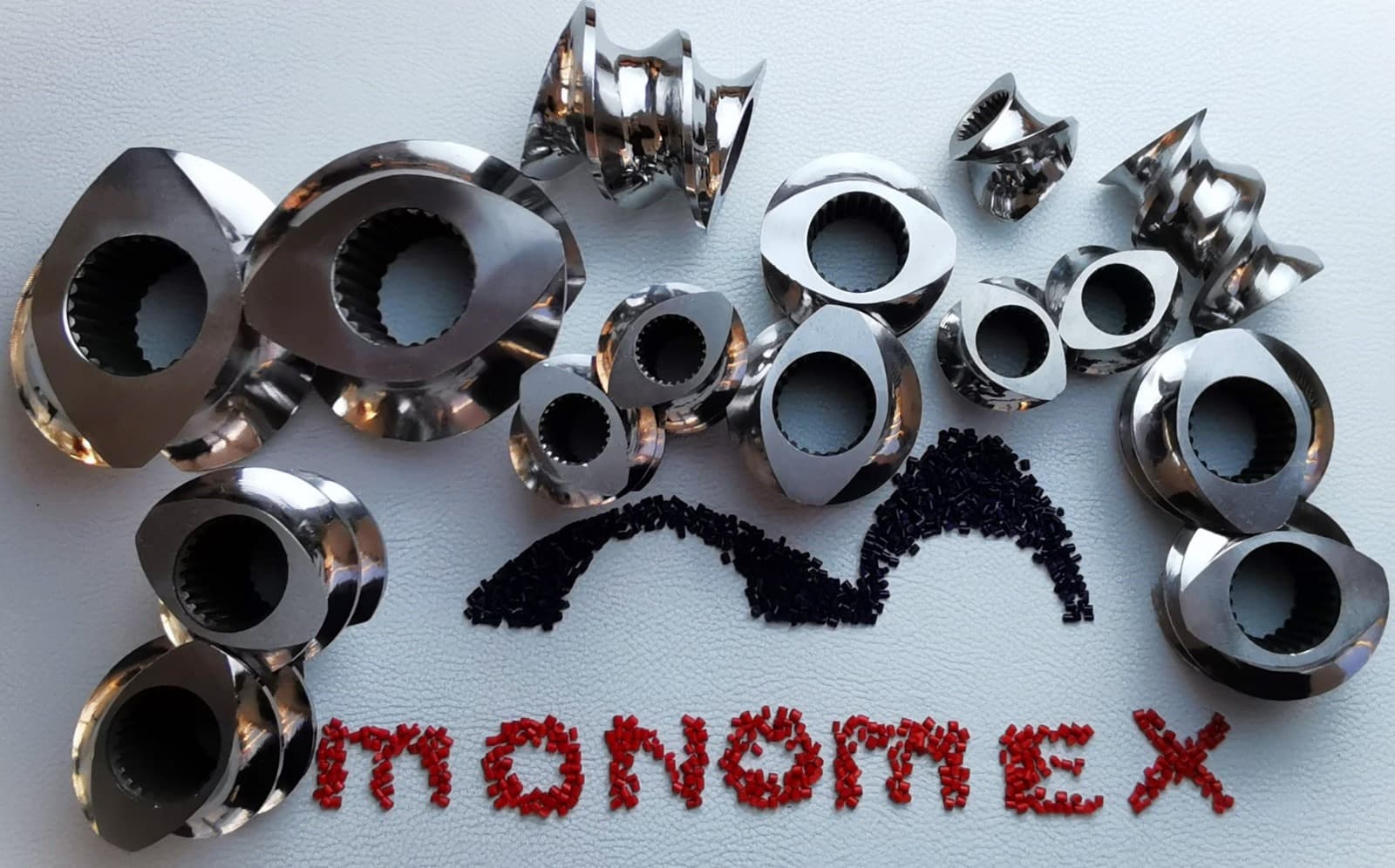
Monomex, the great power behind masterbatch manufacturers, works in the sector to continuously ensure higher quality and more efficient production. The necessary support is provided by Monomex for smart investors who want to make more profitable Masterbatch production. You can make better investments by discussing the chemistry of production with our expert engineer staff on Masterbatch Extruder. General processes where masterbatches are Plastic industry used; injection, blow molding, film, extrusion (sheet, profile), calender, rotation. Masterbatch pallets can be used as colorants and property changers in Polyethylene, Polypropylene, Polystyrene, ABS, EVA, engineering plastics and special compounds. Masterbatches; Various productions are available as organic pigment masterbatches, inorganic pigment masterbatches and mineral fillers, additive masterbatches, black masterbatch, white masterbatch. Please contact us for information on how these productions are carried out and how to choose the right machine.
If we explain what Masterbatch is and give the real recipe for Masterbatch production: Masterbatches are produced with a combination of high-performance organic and inorganic pigments and original polymer raw materials. In antisplit masterbatch production, it is the masterbatch obtained by loading a high amount of filler material into the main carrier raw material, as in normal masterbatch production. The filling materials used here are generally Calcite (CaCO3) and talc materials. It is difficult to reconcile two different materials with each other. For this reason, the choice of machine and the additives used are important factors in facilitating production, increasing the amount of filling materials loaded and product quality. Various additives are used in making antisplit masterbatch. These are PE wax, Zinc stearate, calcium stearate. Particularly the solvent in the wax should be taken into consideration and wax with a solvent with a high auto-ignition temperature should be used.
To give an example formulation:
25% LLDPE (50MFI)
70% Calcite (CaCO3)
2.5% PE Wax
1.5% Zinc Stearate
1% Optical Additive
In all formulations, the fluidity of the masterbatch must be higher than the fluidity of the raw material to be dyed. The masterbatch production process is divided into two parts: Mono and tailor made. In mono production, primary colors are used. In tailor made, that is, color matching, colors are mixed and production is made according to the desired color code.
Three methods in masterbatch production
1:
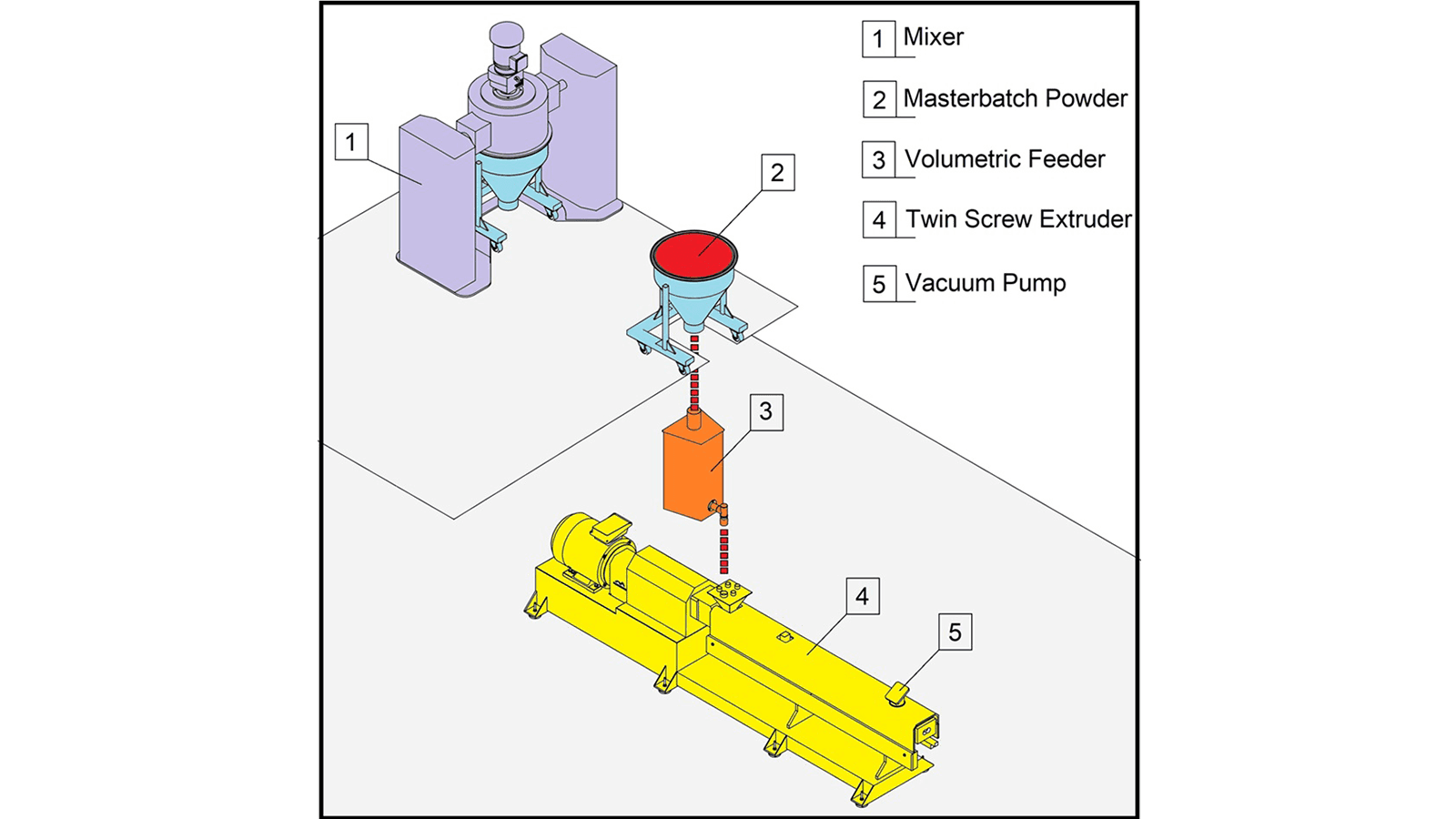
Pre- mix, most widely spread production process, a premix consisting of polymer, pigment and dispersion additives is fed to the extruder. Normally, these premixes are produced in batches in a previous mixing step. Great importance must be given to this premix process. If a mistake happens here, unfortunately, oftentimes it is very difficult to make corrections during the extrusion step. Due to the usage of volumetric feeders, there is a high operational reliability, handling is quite uncomplicated, and the process is very popular as well as low priced.
2:
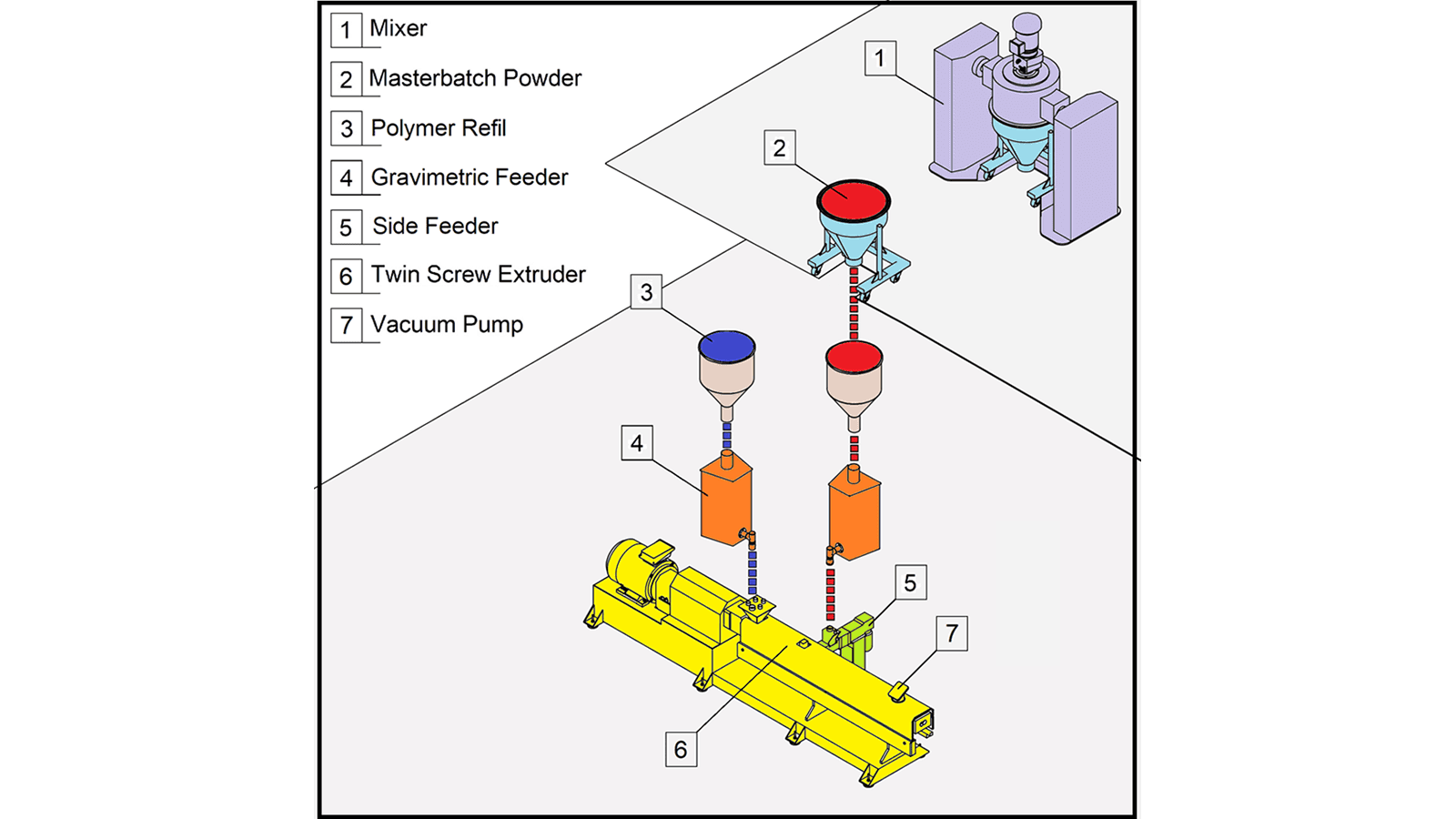
Split-feed version of masterbatch production, the polymer is plastified first. Then the other formulation components (pigments, fillers and if needed dispersion aids) are added via one or two side stuffers (hot melt extrusion). Feeding is done via separate gravimetric feeders. The handling of the formulation via the extruder or feed control is relatively uncomplicated and does not need elaborate premixing. This makes big scale masterbatch production much easier.
3:
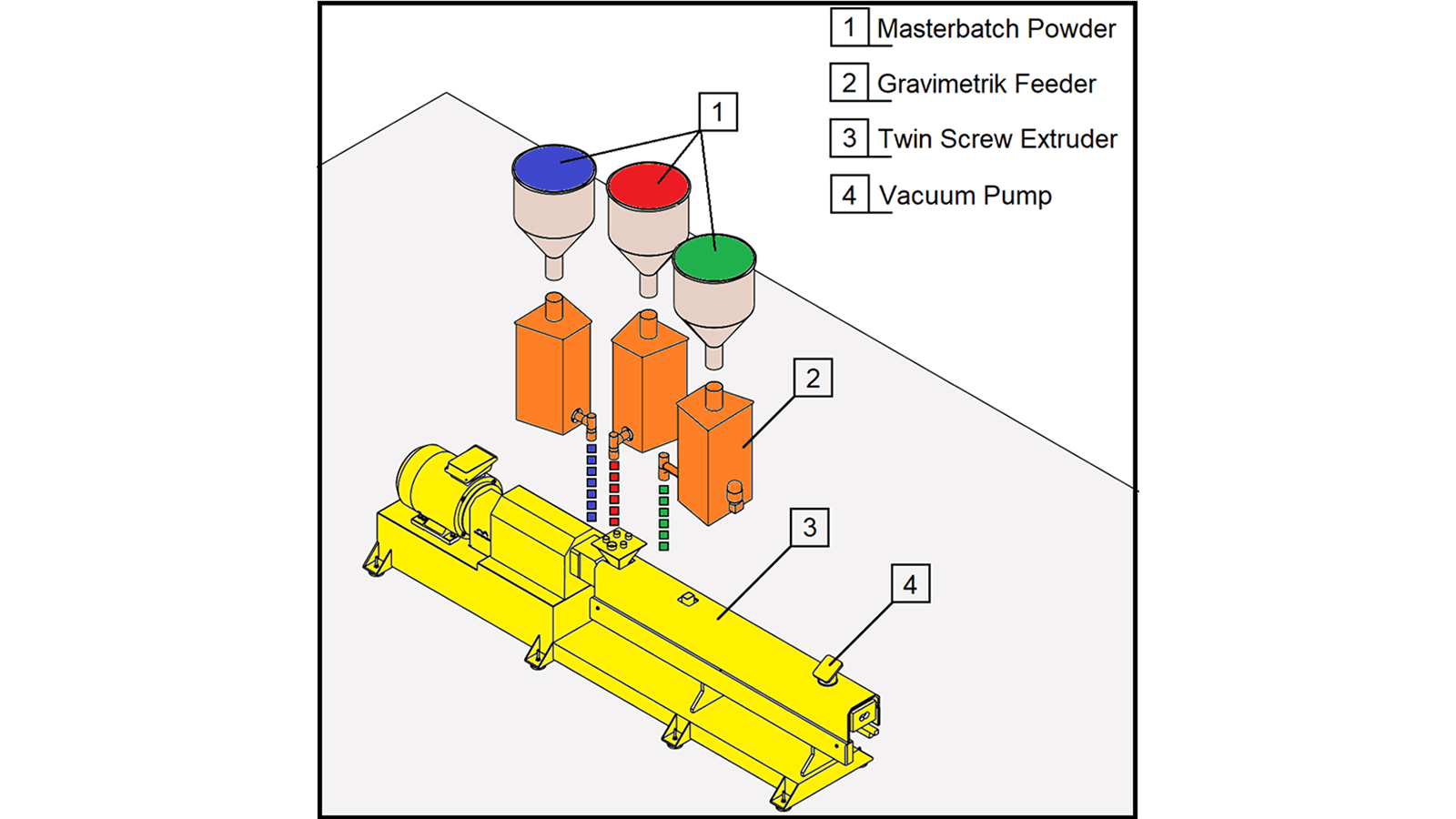
Custom Colouring uses an exact mixture of standard colours (monobatches) to produce the required colour match. Via a multi-component gravimetric feed system (generally 5 to 8 components) and predefined standard colours, the colour required by the customer is produced. The setup of the extrusion line is similar to the premix system.
We can offer the perfect machine configuration for your range of masterbatch formulations, Whether premix or split-feed or color-matching process, with our twin screw extruder. Masterbatch production process for which you are targeting the right about that , please contact our company , which used the method.
What is masterbatch?
Masterbatch is a concentrated mixture of pigments, additives or dyes in a carrier resin. It is used in the plastics industry to add colour or specific properties to plastic materials during the manufacturing process. The carrier resin in masterbatch is usually compatible with the base resin of the final plastic product.
Masterbatch is created by homogeneously dispersing pigments, additives or dyes into the carrier resin using special equipment. This process ensures a homogeneous distribution of the colour or additives throughout the masterbatch. The resulting masterbatch is usually in a solid form in the form of granules or pellets.
During the plastic production process, the masterbatch is mixed with the base resin in specific proportions to achieve the desired colour or properties. The masterbatch is added to the base resin during the extrusion process or in the injection moulding machine. The heat and shear forces applied during processing melt the carrier resin and disperse the pigments or additives into the base resin, resulting in a homogeneous coloured or modified plastic material.
Masterbatch offers several advantages in the plastics industry. The dense pigments ensure colour control by providing consistent and vibrant colour shades. It also enables functional additives such as UV stabilisers, flame retardants, antistatic agents or impact modifiers to be incorporated into the plastic material, thus enhancing its performance characteristics. Furthermore, the use of masterbatch eliminates the need to process and store multiple individual additives, increasing production efficiency and reducing the risk of dosing errors.
Masterbatch is widely used in various industries such as packaging, automotive, construction, consumer products and textiles. It provides manufacturers with a cost-effective and efficient way to add colour and desired properties to plastic materials, offering customisation and meeting specific application requirements.
Masterbatches in Plastic Industry
In the plastics industry, masterbatches are widely used for colouring, property enhancement and functionality in a variety of applications. Here are some of the uses of masterbatches in the plastics industry:
1. Colouring: Masterbatches are used to add desired colours to plastic materials. Coloured masterbatches can be used to provide a specific shade of colour or mixtures of colours. This increases the visual appeal of plastic products and offers the possibility to reflect brand identity.
2. UV Stabilisation: Masterbatches are used to add UV stabilisation properties to protect plastic materials against sunlight or other UV sources. This increases the UV resistance of plastic products and reduces negative effects such as colour fading or material degradation.
3. Flame Retardancy: Masterbatches are used to add flame retardant properties to improve the fire resistance of plastic materials. This improves fire safety and reduces the rate at which plastic products spread during a fire.
4. Anti-Static: Masterbatches are used to provide anti-static properties to reduce or prevent electrostatic build-up on the surface of plastic materials. This reduces the accumulation of dust or dirt on plastic products and prevents problems due to static electricity in electronic devices.
5. Anti-Bacterial: Masterbatches are used to add anti-bacterial properties to prevent or reduce bacterial growth on plastic products. This is an important property in plastics used in hygienic products, food packaging and medical applications.
6. Anti-Oxidant: Masterbatches are used to provide anti-oxidant properties to increase the resistance of plastic materials to oxidation processes. This slows down the ageing processes of plastic products and increases the durability and lifetime of the material.
This is just some of the uses of masterbatches in the plastics industry. Masterbatches can also be used to add various other properties to plastic materials and can be customised according to application needs.
Black Masterbatch
Black masterbatch is an additive used to give plastic materials a black colour. Here are the general properties of black masterbatch:
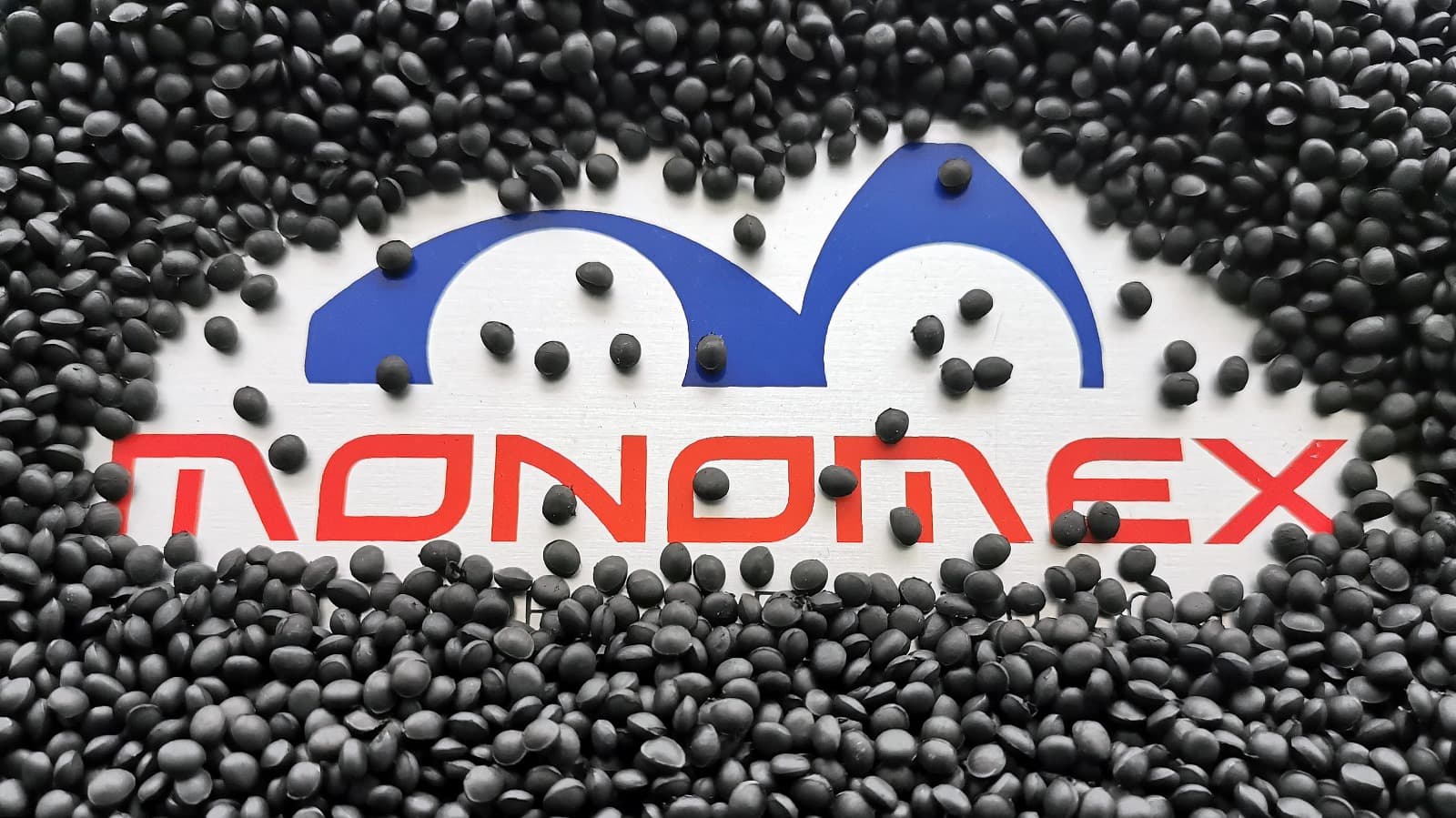
1. Colour Strength and hiding power: Black masterbatch has a high colour strength. This can give the plastic material an intense black colour even when used in low quantities. The colour strength depends on the quality and concentration of the pigment used, such as black carbon pigment. The most commonly used Carbon Black types in black masterbatch production are N115, N220, N330, N550, N772. As the average particle diameters of Carbon Black decrease, the proportion of carbon black that can be loaded into the masterbatch decreases. In other words, while 50% masterbatch can be drawn with N770 carbon, 40% masterbatch can be drawn with the finer structured N330 carbon. More than this, problems may occur in terms of dispersion and carbon distribution.
2. UV Resistance: Black masterbatch can make plastic materials resistant to UV rays. The black carbon pigment protects materials from UV damage by absorbing UV rays. This is an important advantage in applications where materials are exposed outdoors or to sunlight. N110 carbon black with a small structure will provide more excellent UV protection than N990 carbon black. As a result, when choosing the type of carbon black, a preference should be made by considering how much sunlight the product will be exposed to. Another important parameter affecting the UV protection that carbon black will provide in the product is the dispersion of carbon black in the product. The more homogeneously the carbon black is distributed in the product, the more successful it will be in capturing the sun's rays, so the more UV protection will be provided.
3. Dispersion Feature: The black masterbatch is dispersed homogeneously in the plastic material. A good dispersion ensures an even distribution of the black pigment and ensures colour consistency. Homogenous dispersion ensures consistency in the appearance and quality of the products. The ability of a carbon black to disperse well in the product with current production techniques depends on 2 parameters. The smaller the carbon particle size, the more difficult it will be to disperse the carbon black well. Likewise, carbon blacks with a low structure chain will be more difficult to disperse in the product than high structure carbon blacks. Therefore, for example, when using a twin screw extruder rotating in the same direction, the crushing tools on the screw must be well designed. Since there will be more voids in high structure carbon blacks, the carrier polymers will be better inhaled into the carbon black. Thus, a better dispersion can be achieved. As a result, with a properly designed twin screw extruder, good dispersion and smaller diameter carbon blacks are needed for strong UV resistance and better colour tone. Although the dispersion ability of small diameter carbon blacks is difficult compared to large diameters, with a good and effective production technique, homogeneous dispersion can be achieved, resulting in a strong black colour tone and good UV Protection.
4. Chemical Compatibility: The black masterbatch must be compatible with the carrier resin used. The carrier resin ensures that the black masterbatch combines well with the plastic material. This does not affect the strength, flexibility and other physical properties of the material.
5. Thermal Stability: The black masterbatch should have a structure that can remain stable at high temperature. It must be able to withstand the high temperatures that plastic materials are exposed to during processing and during use. Thermal stability affects the performance and processability of the material.
6. Chemical Resistance: Black masterbatch should be resistant to various chemical substances. Chemical resistance is important in applications where plastic materials come into contact with industrial chemicals, acids, bases and other substances. Black masterbatch can increase the chemical resistance of the material.
These properties may vary according to the demands of manufacturers and application requirements.
White Masterbatch
White masterbatch is an additive used to give white colour to plastic materials. Here are the general characteristics of white masterbatch:
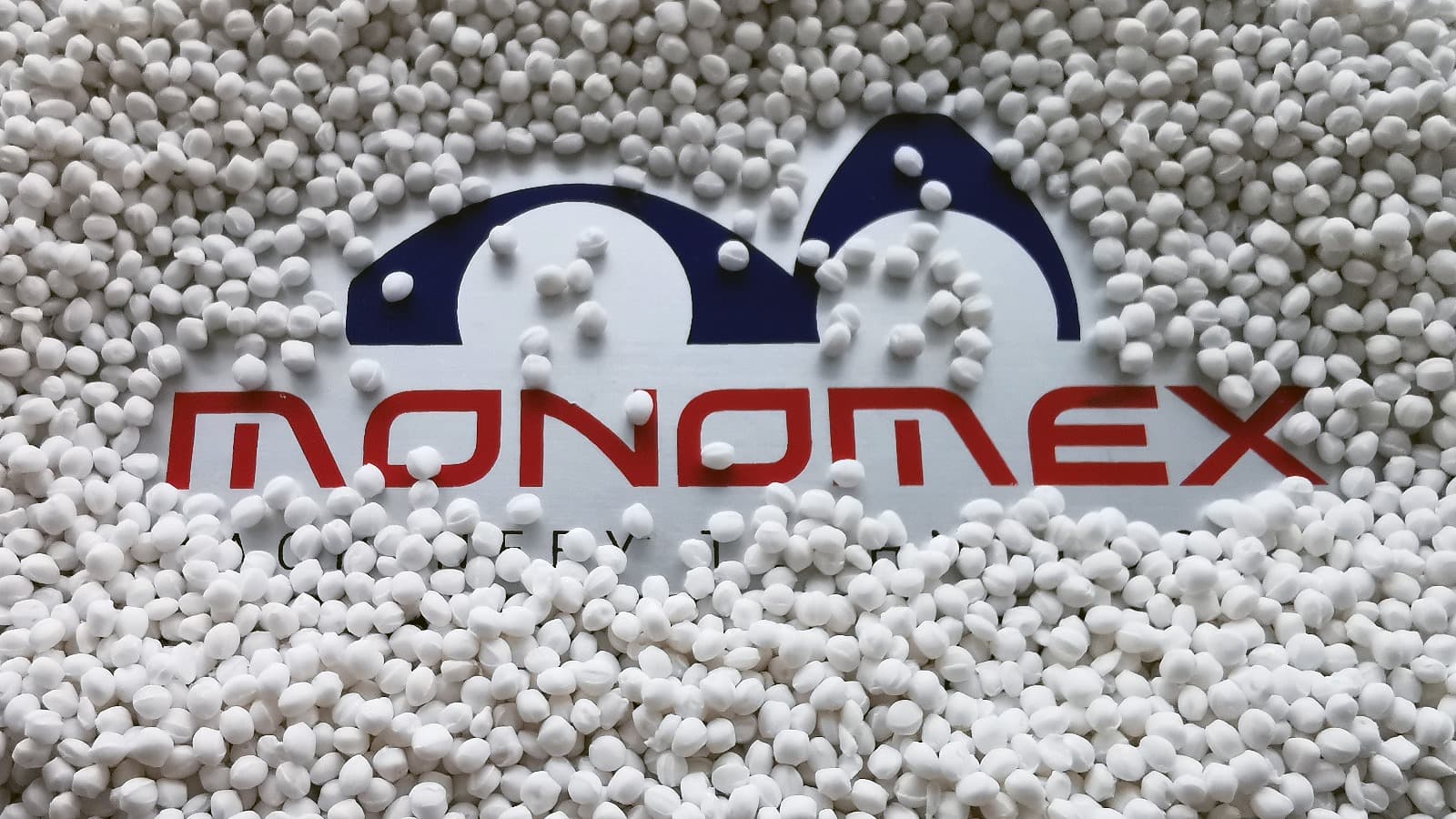
1. Colour Strength: White masterbatch has high colour strength. This can give the plastic material an intense white colour even when used in low quantities. The colour strength depends on the quality and concentration of the white pigment used.
2. Opacity: White masterbatch provides high opacity in plastic materials. That is, it ensures that colours or patterns underneath the material are not visible. This feature allows materials to gain an opaque or opaque white appearance.
3. Dispersion Feature: The white masterbatch is dispersed homogeneously in the plastic material. A good dispersion ensures an even distribution of the white pigment and provides colour consistency. Homogeneous dispersion ensures consistency in appearance and quality of products.
4. UV Resistance: Some white masterbatches can be specially formulated to provide resistance to UV rays. This prevents discolouration or degradation in applications where materials are exposed outdoors or to sunlight.
5. Chemical Compatibility: The white masterbatch must be compatible with the carrier resin used. The carrier resin ensures that the white masterbatch combines well with the plastic material. This does not affect the strength, flexibility and other physical properties of the material.
6. Thermal Stability: The white masterbatch should have a structure that can remain stable at high temperature. It must be able to withstand the high temperatures that plastic materials are exposed to during processing and during use. Thermal stability affects the performance and processability of the material.
7. Chemical Resistance: White masterbatch should be resistant to various chemical substances. Chemical resistance is important in applications where plastic materials come into contact with industrial chemicals, acids, bases and other substances. White masterbatch can increase the chemical resistance of the material.
These properties may vary according to the demands of manufacturers and application requirements.
Colour Masterbatch
Colour masterbatch is a type of additive used to add a desired coloured appearance and aesthetics to plastic materials. Colour masterbatches can be available in different colours and are commonly used in the plastics industry. Here are the general characteristics of colour masterbatches:
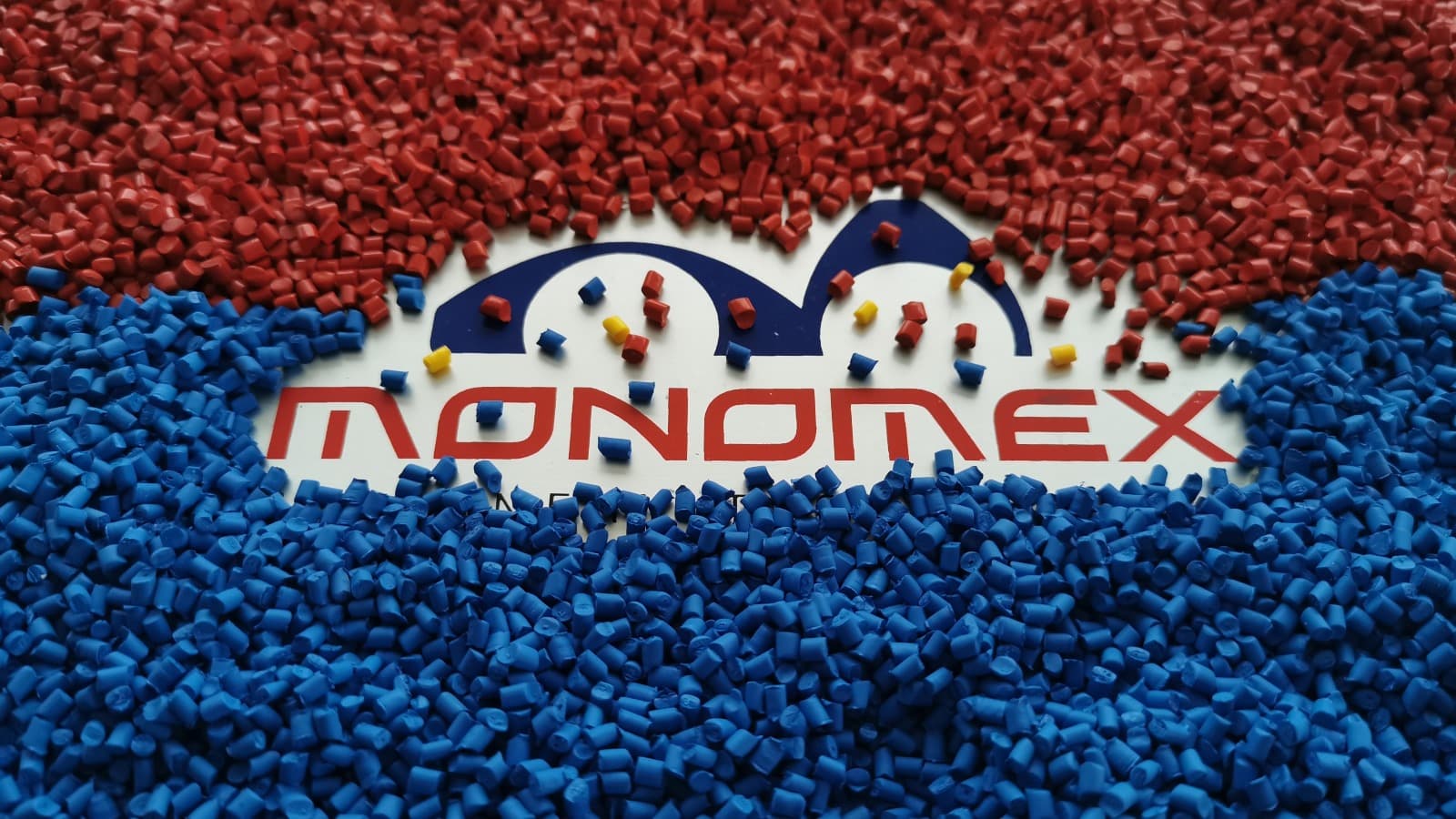
1. Colour Strength and Accuracy: Colour masterbatches have high colour strength. This means that they are capable of imparting an intense colour to the plastic material even when used at a low rate. They also provide colour accuracy, i.e. they are suitable for consistently achieving the desired colour shade.
2. Dispersion Property: Colour masterbatches are dispersed homogeneously in the plastic material. A good dispersion ensures an even distribution of the colour pigments and improves colour consistency. Homogenous dispersion ensures consistency in the appearance of production parts and products.
3. Compatible Carrier Resin: Colour masterbatches must be compatible with the carrier resin used. This ensures that the colour masterbatch mixes and merges well with the plastic material. A compatible carrier resin provides the desired colour tone without affecting the physical properties and performance of the material.
4. Chemical Resistance: Colour masterbatches, plastic materials must be resistant to chemicals, acids, bases and other chemical agents. This ensures durability and longevity of the materials.
5. UV Resistance (optional): Some colour masterbatches can be specially formulated to protect plastic materials against UV rays. This prevents discolouration or degradation in applications where materials are exposed outdoors or to sunlight.
6. Thermal Stability: Colour masterbatches must remain stable at elevated temperatures and maintain their performance under temperature conditions to which plastic materials are exposed during processing or in use.
Colour masterbatches play an important role in enhancing the aesthetic appearance, marketing appeal and brand recognition of plastic products. Colour strength, dispersibility, compatible carrier resin, chemical resistance, UV resistance (where applicable) and thermal stability are the key characteristics of colour masterbatches. These properties are taken into account to determine the quality of the colour masterbatch and the application requirements.