Water Ring Pelletizers
Water Ring Granulating Machine is a system used to turn molten polymer into granules in plastic extrusion processes. This system is especially preferred for thermoplastic materials with high fluidity.
Working Principle:
1) Melting and Extrusion: The polymer material is melted in the extruder and pushed out through the die plate.
2) Cutting Process: The molten polymer that comes out of the mold is cut by rotating blades.
3) Cooling: The cut polymer particles are cooled rapidly by continuous spraying of water on the mold surface. This water also acts as a carrier for the granules and transmits them to the granule collection system.
4) Separation and Drying: The granules in the water are separated from the water by means of a centrifugal dryer or vibrating screens and dried and stored as the final product.
Users' Choice: Functional Reliability, Ease of Use, and Versatility. Granule production has never been this easy.
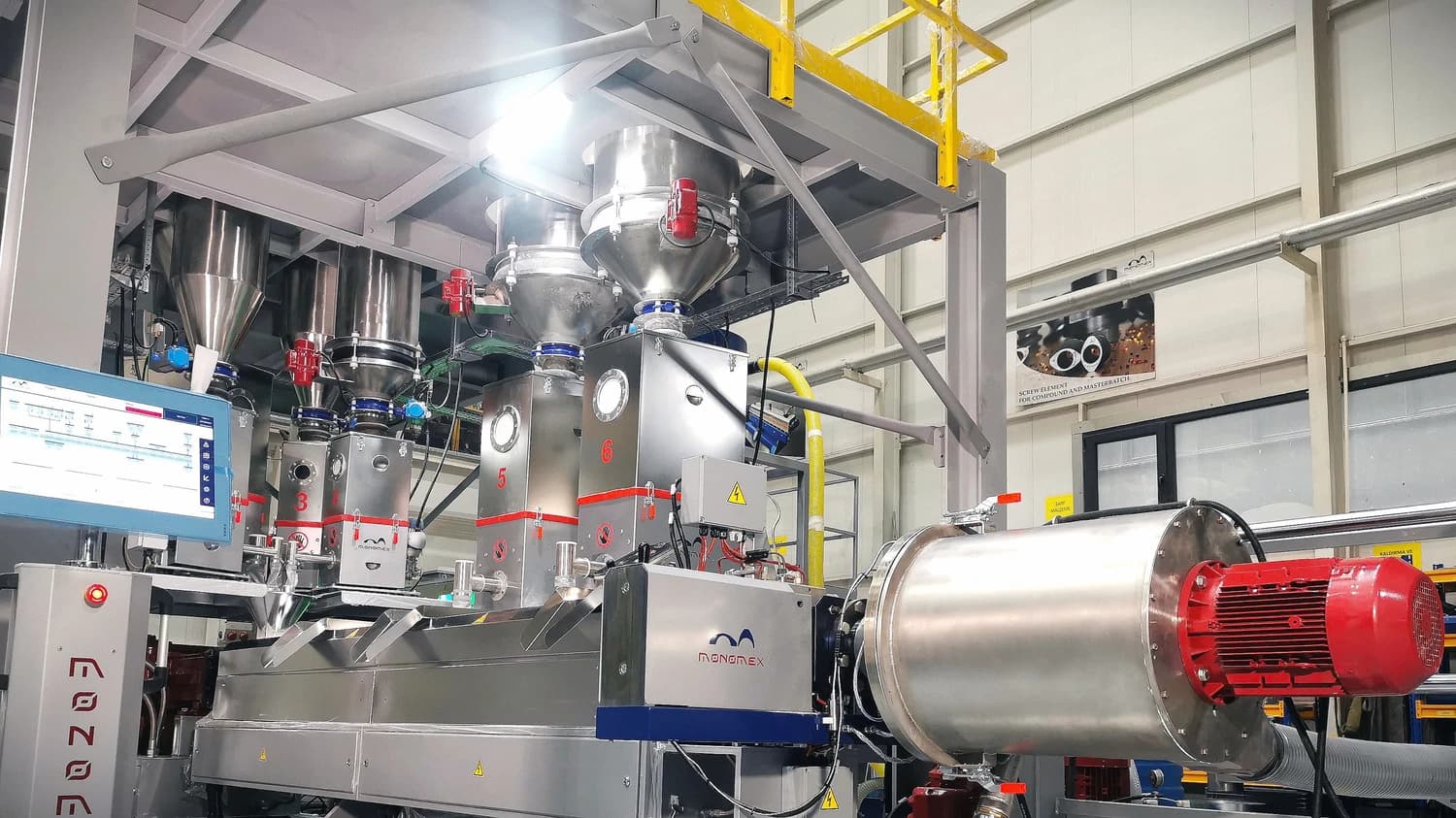
Water ring granule cutting allows you to discover the secrets of excellent extruder granule cutting. This system provides high efficiency for producing high-quality granules and optimizes your business processes.
Water Ring Granule Cutting Technology
The granule production process is enhanced with Direct Drive technology for higher quality. Water ring granule cutting smoothly cuts and converts the material at the extruder exit into the granules. Here are the key features of this technology:
Blade Head Pressure: Maintenance-free and smooth mechanical movement.
Direct-Drive Blade Head Shaft: Provides cutting with high efficiency.
Cutting Pressure Adjustment: Outstanding cutting precision.
Blades and Die Surface: Long-lasting and highly durable.
Advantages
The advantages provided by the water ring granule cutting system are as follows:
Single Cutting Method for Irregular Flow: The only cutting method that can be used when the processed material’s pressure and flow rate variations are significant at the extruder exit.
Uniform Granule Size: The granules become homogeneous and round in shape, which increases processability.
Continuous Production: It's a system suitable for continuous operation.
Wide Material Compatibility: It can work with a wide range of plastics such as PE, PP, PVC, PET, ABS, PS. It can be used in a variety of the systems.
Less Dust Formation: Minimum dust formation is ensured thanks to the water-cooled system.
Low Investment and Operating Costs: Keeps your business costs low.
Dust-Free Product: No dust is generated during the cutting process.
Space-Saving: Efficient use of factory space due to its small footprint.
Low Energy Consumption: Energy costs are reduced because the heat transfer to the cooling water is minimal.
Ergonomic Design: Personnel work with less effort, thereby increasing efficiency.
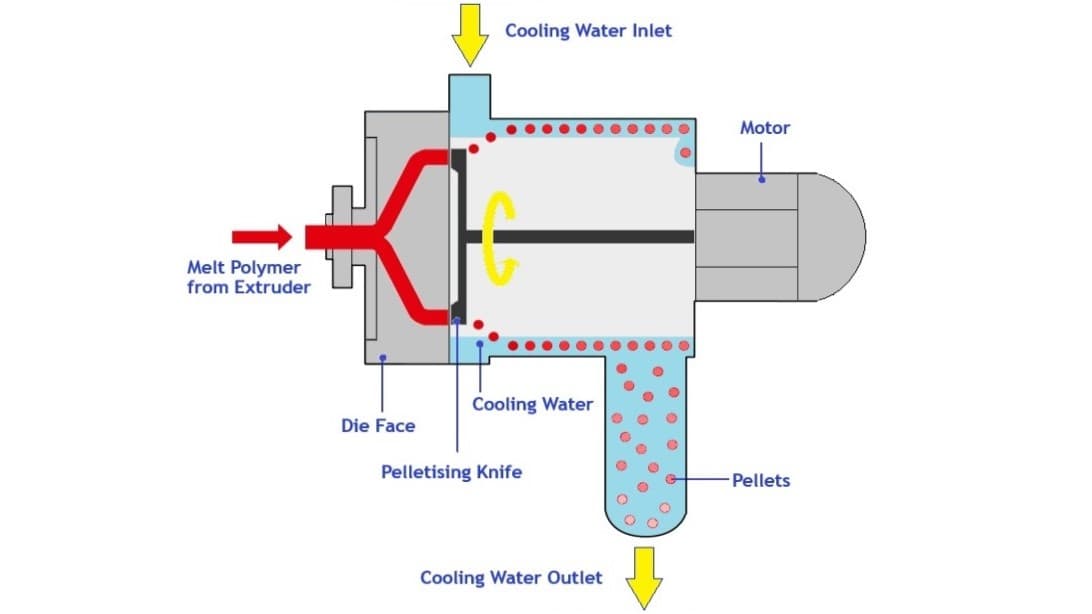
Design Differences
The design differences offered by the water ring granule cutting system are as follows:
Homogeneous Product Production: A more homogeneous product structure is achieved.
Reduced Water Consumption: Process water consumption has been minimized.
Minimal Waste During Material Change: Minimal waste is ensured during material changes.
New Type of Blades: New blades with increased durability are used.
Ease of Use: User-friendly design ensures ease of operation.
Increased Workplace Safety: Workplace safety is prioritized.
Water Ring Granule Cutting Process
Water ring granule cutting is used to convert the molten material exiting the extruder into spherical form. The molten material exiting the extruder molds is cut by rapidly rotating blades, falls into a ring-shaped water flow, cools down, and takes on a spherical shape. In this cutting system, water flows in a ring around the blades, which is why this system is called "water ring granule cutting".
Technical Specifications
The technical specifications of the water ring granule cutting machines are as follows:
Applications
1) Plastic recycling lines.
2) Masterbatch production.
3) Polymer compound production.
4) Processing of low viscosity materials.
5) This system is especially suitable for medium and high capacity productions and provides high performance with energy efficiency.
Granule systems cut from the hot mold surface can generally be used for all traditional thermoplastic melts, except for PA 6.6, PET, and PP melts with an MFI (Melt Flow Index) greater than 250 g/10 minutes.