Strand Pelletizers
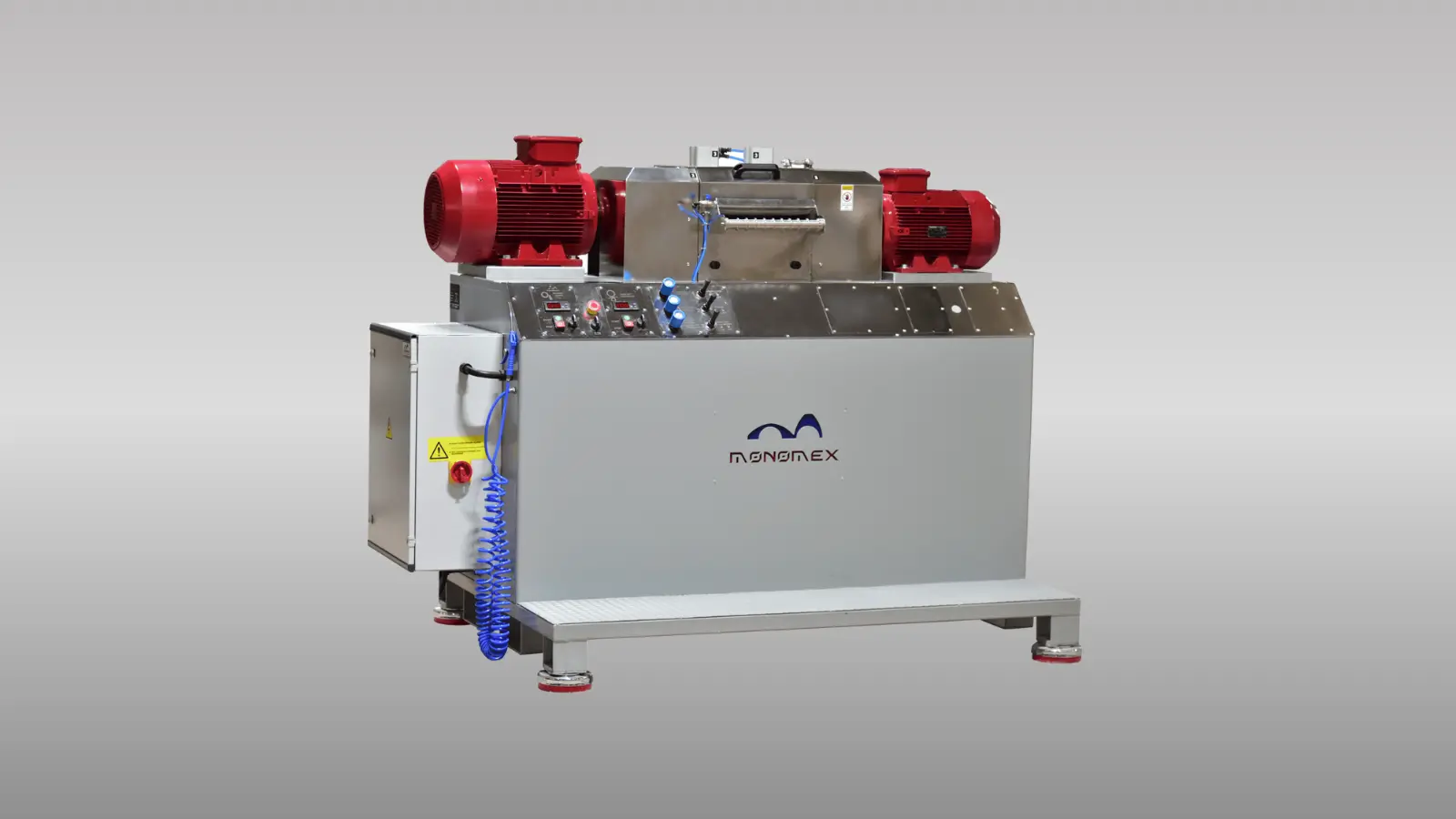
DRY CUT STRAND PELLETIZER PROCESS
The material, which exits the extruder in a molten state, is transformed into thin rods in the cooling tank. Then, it is turned into cylindrical pellets through the Dry Granule Cutting Machine (Granulator).
Suitable for fixed 3mm length and 3mm diameter granule cutting. During cutting, the material enters the blades dry. It's the most frequently used cutting method. If the material to be cut is not of proper quality, it tends to break or not in the form of standart granules. In this way, the quality of the melt material is also revealed.
The drawing roller in the machine applies an ideal pulling force to the thin rods. The success of the cutting process depends on the material's mechanical properties:
Very hard materials: Cause brittleness.
Very soft materials: Lead to a chewing effect instead of cutting.
For the right equipment selection, you can consult with our expert engineers to determine the properties of the drawing roller and the knife geometry.
MICRO CUT STRAND PELLETIZER PROCESS
Suitable for cutting to 3mm under or above lenght. It's usually used for cutting 1 mm lenght. It's mainly used in areas where the Masterbatch is required to melt quickly, shortening the dying time and uniform distribution.
UNDERWATER STRAND PELLETIZER PROCESS
Suitable for cutting materials which tend to break continuously. The melt wicks coming out of the extruder die fall into the flowing water in a sloping manner. The falling material proceeds with the flow of water towards to the Granulator. There is no operator intervention in the melt material going from Extruder to Granulator. The wicks that enter the granulator with water are separated from the water during cutting.
Technical Specifications
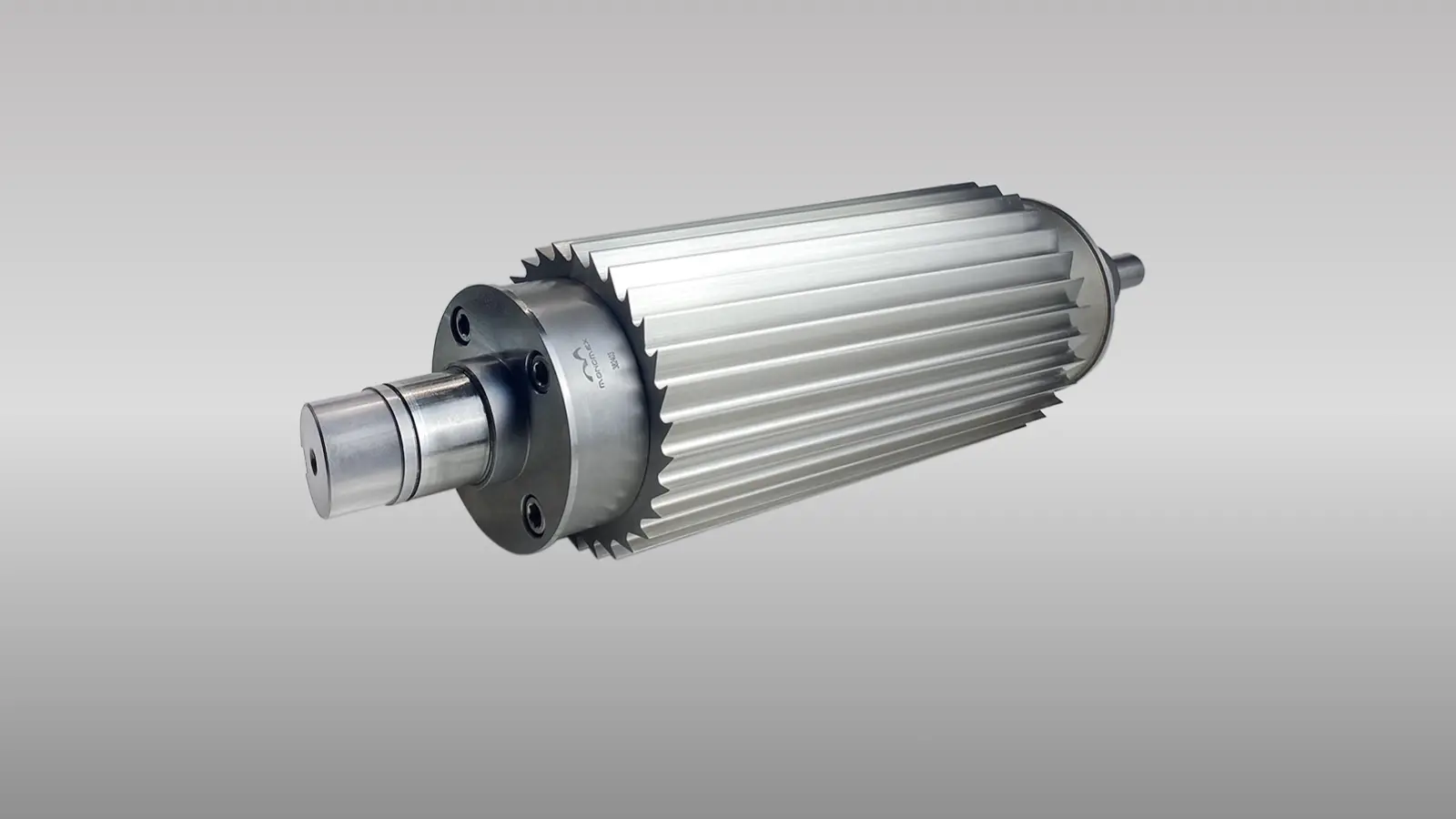
Advantages
Quick and Easy Cleaning: It is the fastest and easiest cutting system for cleaning during product changeovers.
Error Detection: Immediate quality control of the product exiting the extruder minimizes production errors.
Solution for Tough Materials: High cutting performance with tough materials such as glass fiber-reinforced materials.
Low Investment Cost: Provides high performance at an affordable cost.
Easy Drying: The moisture content of the product can be easily controlled.
Design Features
Workplace Safety: User-friendly and safe design.
Ergonomic Blade Replacement: Easy access for intervention.
Long-Lasting Blades: Blade geometry and profiles enhance the cutting lifespan.
Optional Features: Additional options are available based on customer needs.
Expert Blade Sharpening Service
Monomex enhances the sharpness life of cutting blades with its original profile sharpening service, maximizing production efficiency.
PM (Powdered Metal) or Carbide Blades: High performance for hard materials.
Correct Blade Angle: Perfect cuts with blades optimized for the product.
Choose Monomex Dry Granule Cutting Systems for high efficiency and waste-free production. Contact our experts for more information!